How to Install Bucket Teeth on Your Excavator
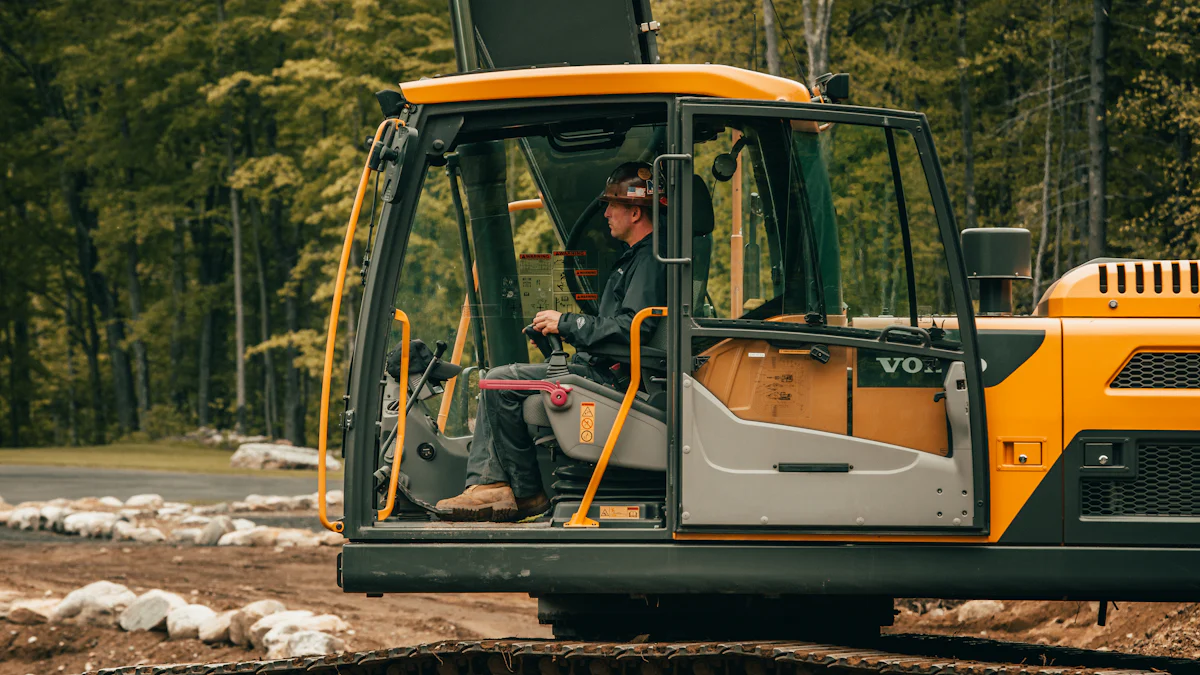
Installing bucket teeth on your excavator is a crucial task that directly impacts the machine’s performance. Proper installation ensures that the teeth function optimally, enhancing digging efficiency and extending their lifespan. You need to follow the correct procedures to avoid potential damage or injury. Using the right tools and techniques, you can secure the teeth effectively. This process not only boosts the excavator’s productivity but also reduces the frequency of replacements. Remember, a well-installed set of bucket teeth can make a significant difference in your excavation projects, much like the Motor Grader Cutting Edge enhances grading tasks.
Choosing the Right Tools
Selecting the appropriate tools is crucial for installing bucket teeth on your excavator. The right tools ensure a smooth installation process and enhance the performance of your machine.
Essential Tools
To begin, gather the essential tools needed for the task:
Hammer
A hammer is indispensable for installing bucket teeth. You will use it to secure the retainer and pin set, ensuring the teeth stay firmly in place. Choose a sturdy hammer that can withstand repeated use.
Retainer and Pin Set
The retainer and pin set is vital for attaching the bucket teeth securely. This set includes the components necessary to lock the teeth onto the bucket. Make sure you have the correct size and type for your specific excavator model.
Safety Gear
Safety should always be a priority. Equip yourself with safety gear such as gloves and goggles. These items protect you from potential injuries during the installation process.
Optional Tools
While not mandatory, optional tools can make the installation process easier and more efficient:
Lubricant
Using a lubricant can facilitate the insertion of pins and reduce friction. It helps in achieving a snug fit without excessive force. Apply a small amount to the pins before installation.
Cleaning Brush
A cleaning brush is useful for removing dirt and debris from the bucket and adapter. A clean surface ensures a better fit for the new teeth and prevents premature wear. Regular cleaning also helps in maintaining the overall condition of your excavator.
By preparing these tools, you set the stage for a successful installation. Properly installed bucket teeth improve your excavator’s efficiency and longevity, making your excavation projects more effective.
Preparing the Bucket
Cleaning the Bucket
Proper preparation of your excavator bucket begins with cleaning. A clean bucket ensures a secure fit for the new teeth and prevents premature wear.
Removing Dirt and Debris
Start by removing any dirt and debris from the bucket. Use a cleaning brush to scrub away loose particles. This step is crucial because accumulated dirt can interfere with the installation process. A clean surface allows the teeth to fit snugly, enhancing their performance.
Inspecting for Damage
After cleaning, inspect the bucket for any signs of damage. Look for cracks, dents, or wear that might affect the installation. Identifying and addressing these issues early can prevent further damage and ensure the longevity of your bucket. If you find any significant damage, consider consulting a professional for repairs before proceeding with the installation.
Positioning the Bucket
Once the bucket is clean and inspected, position it correctly for the installation of the teeth. Proper positioning is essential for safety and ease of access.
Stabilizing the Excavator
Stabilize the excavator to prevent any movement during the installation. Engage the parking brakes and use jack stands or wooden blocks as secondary support. This precaution helps prevent accidents, such as pinching or crushing incidents, ensuring a safe working environment.
Ensuring Accessibility
Ensure that the bucket is accessible and positioned correctly. The bucket should face upwards with the teeth parallel to the ground. This alignment facilitates easy access to the attachment points and ensures that the teeth are installed correctly. An empty bucket prevents any materials from falling out during the process, further enhancing safety.
By thoroughly preparing the bucket, you set the stage for a successful installation. These steps not only ensure a secure fit for the new teeth but also contribute to the overall maintenance and care of your excavator bucket, extending its lifespan and maintaining optimal performance.
Installing the Retainer
Proper installation of the retainer is crucial for securing the bucket teeth on your excavator. Follow these steps to ensure a successful installation.
Aligning the Retainer
Aligning the retainer correctly is the first step in the installation process. This ensures that the teeth will be securely attached and function effectively.
Positioning Correctly
Begin by positioning the retainer in its designated slot on the bucket. Make sure it sits flush against the surface. This positioning is essential for the stability of the teeth. A misaligned retainer can lead to loose teeth, which may affect the excavator’s performance.
Checking Alignment
After positioning, check the alignment of the retainer. Look from different angles to ensure it is straight and centered. You can use a straight edge or a level to verify this. Proper alignment prevents uneven wear and ensures that the teeth distribute force evenly during operation.
Securing the Retainer
Once aligned, you need to secure the retainer firmly. This step is vital for maintaining the integrity of the installation.
Using the Hammer
Use a hammer to tap the retainer into place. Apply firm, even pressure to avoid damaging the retainer or the bucket. The hammer helps lock the retainer securely, ensuring it does not shift during use. Choose a hammer that is comfortable to handle and provides adequate force.
Ensuring a Tight Fit
Finally, ensure a tight fit by checking the retainer’s stability. It should not move or wiggle when touched. If necessary, give it a few more taps with the hammer. A tight fit guarantees that the teeth remain secure, reducing the risk of them coming loose during excavation tasks.
Expert Testimony: Dr. Lyuba Taft, an expert in orthodontics, emphasizes the importance of choosing the right retainer for optimal performance. Similarly, selecting and securing the correct retainer for your excavator ensures the best fit and functionality.
By following these steps, you ensure that the retainer is installed correctly, providing a solid foundation for the bucket teeth. This careful attention to detail enhances the overall efficiency and longevity of your excavator.
Inserting and Securing the Pin
Inserting the Pin
Proper pin insertion is crucial for securing the bucket teeth on your excavator. Follow these steps to ensure a successful installation.
Aligning with the Retainer
Begin by aligning the pin with the retainer. This alignment is essential for a secure fit. Position the pin so it matches the holes in the retainer and the bucket. Ensure that the pin is straight and centered. Proper alignment prevents unnecessary stress on the pin and ensures even distribution of force during operation.
Ensuring Proper Placement
Once aligned, insert the pin into the retainer. Push it through until it fits snugly. Make sure the pin is fully seated in its slot. A properly placed pin enhances the stability of the bucket teeth. It also reduces the risk of the teeth coming loose during excavation tasks.
Securing the Pin
After inserting the pin, you need to secure it firmly. This step is vital for maintaining the integrity of the installation.
Hammering the Pin
Use a hammer to drive the pin into place. Apply firm, even pressure to avoid damaging the pin or the retainer. The hammer helps lock the pin securely, ensuring it does not shift during use. Choose a hammer that is comfortable to handle and provides adequate force.
Professionals in the field of orthopedic trauma emphasize the importance of proper pin insertion techniques. They note that the correct approach ensures stability and prevents complications. Similarly, using the right technique when hammering the pin ensures a secure fit for your excavator’s bucket teeth.
Checking for Stability
Finally, check the stability of the pin. It should not move or wiggle when touched. If necessary, give it a few more taps with the hammer. A stable pin guarantees that the teeth remain secure, reducing the risk of them coming loose during excavation tasks.
Authors of a biomechanical analysis study highlight that pin selection and insertion technique are crucial for achieving a stiff construct. In the context of excavators, ensuring the pin’s stability is key to maintaining the efficiency and longevity of the bucket teeth.
By following these steps, you ensure that the pin is inserted and secured correctly. This careful attention to detail enhances the overall efficiency and longevity of your excavator.
Motor Grader Cutting Edge
Understanding the role and maintenance of the Motor Grader Cutting Edge is essential for anyone involved in excavation and grading tasks. This component plays a pivotal role in ensuring your equipment performs efficiently and effectively.
Understanding the Role
The Motor Grader Cutting Edge is crucial for scraping, leveling, and smoothing uneven surfaces. It acts as the primary contact point between the grader and the ground, making it indispensable for achieving a smooth finish on various terrains. Different types of cutting edges are available, including those made from through-hardened medium carbon DH-2 steel, which offer enhanced durability and performance. By selecting the appropriate cutting edge for your specific needs, you can significantly improve the productivity of your motor grader.
Key Insight: Ground engaging tools (GET), such as the Motor Grader Cutting Edge, play a significant role in enhancing production and reducing operating costs. They ensure that your equipment can handle tough conditions while maintaining efficiency.
Maintenance Tips
Regular maintenance of the Motor Grader Cutting Edge is vital for ensuring optimal performance and longevity. Here are some essential maintenance tips:
-
Routine Inspection: Regularly inspect the cutting edge for signs of wear or damage. Look for cracks, chips, or excessive wear that might affect its performance. Early detection allows for timely repairs or replacements, preventing further damage to your equipment.
-
Timely Servicing: Schedule routine servicing to address any issues with the cutting edge. This includes sharpening or replacing worn edges to maintain their effectiveness. Timely servicing ensures that your motor grader continues to operate at peak efficiency.
-
Proper Storage: When not in use, store the cutting edge in a dry, protected area to prevent rust and corrosion. Proper storage extends the lifespan of the cutting edge and maintains its performance.
Maintenance Insight: Altering the cutting edge can impact digging performance and wear resistance. Regular maintenance and timely repairs are crucial for safety and performance, ensuring that your motor grader operates smoothly and efficiently.
By understanding the role and following these maintenance tips, you can ensure that your Motor Grader Cutting Edge remains in excellent condition. This attention to detail not only enhances the performance of your equipment but also contributes to the overall success of your excavation and grading projects.
Installing bucket teeth on your excavator involves several key steps that ensure optimal performance and longevity. By choosing the right tools, preparing the bucket, and securing the retainer and pin, you enhance the machine’s efficiency. A secure installation reduces maintenance and repair costs, as it minimizes stress on the equipment. Regular maintenance checks are crucial for safety and effectiveness. They help prevent accidents and unexpected failures. Using wear-resistant materials further extends the bucket’s life. By following these guidelines, you maintain your excavator’s productivity and reliability in excavation projects.
Post time: Nov-20-2024